Les aspects techniques : la clé pour bien définir votre projet de nouvelle ligne d’emballage
La décision d’automatiser le système d’emballage final est parfois très claire. Mais souvent, le processus lui-même et le projet d’emballage peuvent sembler compliqués si vous ne savez pas quels éléments et systèmes sont nécessaires. Dans l’article d’aujourd’hui, nous allons aborder les aspects techniques les plus importants d’une nouvelle ligne d’emaballage.
Dans un nouveau projet d’emballage, il y a de nombreux éléments à prendre en compte, parce que, il est important de les classifier par objectifs et par aspects techniques. Dans le cas d’Innova, pour faciliter cette tâche, nous conseillons nos clients à tout moment et nous adaptons à leurs besoins.
1. Objectif principal du projet et planification
Tout d’abord, il faudra être clair sur l’objectif principal du nouveau projet d’emballage, qu’il s’agisse d’une automatisation complète, d’une rénovation des machines existantes ou d’une extension de la ligne. Il est également très important que le fabricant, dans ce cas, Innova Group connaisse le calendrier prévu et, surtout, la date de mise en service prévue.
Bien que cette première étape puisse sembler évidente, la planification est essentielle pour concevoir et optimiser la ligne de conditionnement au maximum de son potentiel.
2. Analyse et propositions pour les systèmes d’emballage
La prochaine étape du nouveau projet consistera à définir les objectifs de conditionnement de la nouvelle ligne afin de déterminer les systèmes de conditionnement qui seront nécessaires. En général, les objectifs les plus courants sont :
- Protection totale et imperméabilité : pour ces objectifs, nous recommandons le système Stretch Hood, car il couvre complètement la charge.
- Support extra et sécurisation pour le transport : pour cela, plusieurs systèmes sont disponibles ; Housseusse Étirable, systèmes de Cerclage, Banderoleuses automatiques en tenant compte des caractéristiques du produit.
- Image de marque et présentation : il s’agit de l’un des objectifs les plus demandés pour offrir une valeur ajoutée de marque au produit. Dans ce cas, nous recommandons le système Stretch Hood pour sa transparence et la possibilité de personnaliser le consommable.
- Economiser les consommables : et pour cela, nous recommandons le système Stretch Hood, car il permet d’économiser jusqu’à 50% de film par rapport à d’autres systèmes tels que la banderoleuse automatique ou semi-automatique.
Après avoir défini la combinaison de systèmes d’emballage qui sera nécessaire, nous passerons au point suivant, à savoir l’emplacement de la ligne.
3. Emplacement de la ligne de d’emballage dans l’usine
Dans chaque projet, nous étudions en détail l’usine, ses espaces et son intégration avec la ligne de production. Donc, il est important que tous les aspects techniques de l’emplacement soient clairs dès le départ. En fonction de l’espace et des connexions avec la production et la sortie de l’entrepôt, Innova élaborera la ligne de transport qui mieux vous convient. Pour assurer une bonne gestion de cette étape, le client doit fournir des informations sur tous les types de travaux effectués ou à effectuer dans l’usine, ainsi que les mesures des autres lignes et véhicules de chargement (chariots élévateurs, AGV, transpalettes, etc.).
Puis, à l’intérieur de l’emplacement, nous aurons des aspects tels que :
- Mesures et hauteurs du local ou du zone où la ligne sera située.
- Environnement d’implantation des machines : environnement froid, tropical, corrosif ou zone ATEX, entre autres.
- Périmètres de sécurité nécessaires.
- Flux de mouvements d’usines.
- Transport et accès aux charges (avec chariots élévateurs, AGV (Automatic Guided Vehicles), etc.)
- Stockage disponible, si nécessaire, pour les consommables.
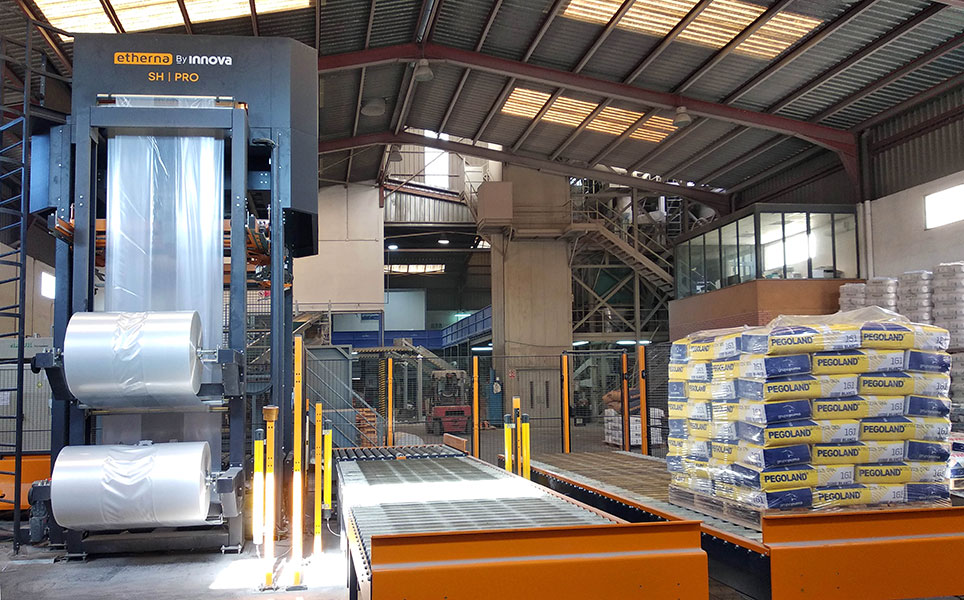
4. Connexion et intégration avec la production et l’entrepôt
Ensuite, nous devons réaliser la connexion à la ligne existante, tant en termes de machines et de systèmes de transport qu’en termes de communication. En termes de transport, Innova travaille principalement avec des systèmes de convoyeur à rouleaux en raison de leur résistance et de leur efficacité avec les palettes lourdes, mais nous adaptons aussi la ligne de conditionnement aux systèmes de transport que le client a installés. Dans ce cas, il est nécessaire de connaître la hauteur des lignes de production et des accès de chargement existants afin de dimensionner la ligne de convoyage.
En ce qui concerne la communication avec la ligne de production et l’entrepôt logistique, nous offrons des intégrations de communication avec les PLC les plus courants du marché, tels que Omron, Siemens, Rockwell ou Schneider, entre autres. De plus, la ligne d’emballage d’Innova est configurée pour l’intégration de solutions intelligentes et de robotique 4.0 qui se connectent directement au CRM (systèmes de gestion et le stockage des marchandises) du client.
Dans cette section, nous devons aussi tenir compte de la connexion avec d’autres systèmes automatiques de fin de ligne tels que les systèmes de pesage ou d’étiquetage en fin de ligne. Ils doivent être inclus dans la conception de ligne et avoir un lien de communication avec l’automate de la ligne.
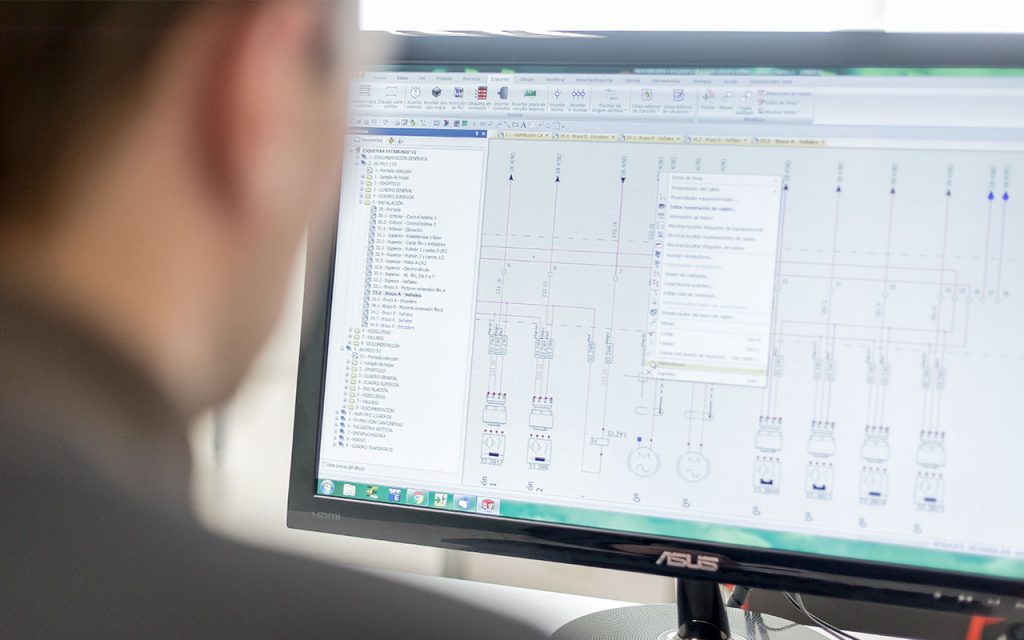
5. Définition du flux et des formats d’emballage
Pour le fabricant, il est très important de connaître le flux de production en fonction des palettes/heure, des formats de palettes (hauteurs et dimensions), des types d’emballages à réaliser, etc. Tout sera nécessaire lors de la définition du projet et aussi lors de la programmation des systèmes d’emballage avec les processus à réaliser.
- Mesures définitives de toutes les charges.
- Dimensions de la base de la palette (s’il y a différents formats)
- Les formats spéciaux, qui nécessitent un emballage différent.
- Mesures et formats des charges qui pourraient arriver à la ligne d’emballage dans un proche avenir.
- Flux de production par heure.
- Flux de palettes sortantes vers l’entrepôt afin de ne pas les accumuler sur la ligne de sortie.
- Intervention d’autres systèmes sur la ligne (comme l’étiquetage ou la pesée pendant ou à la fin de l’emballage).
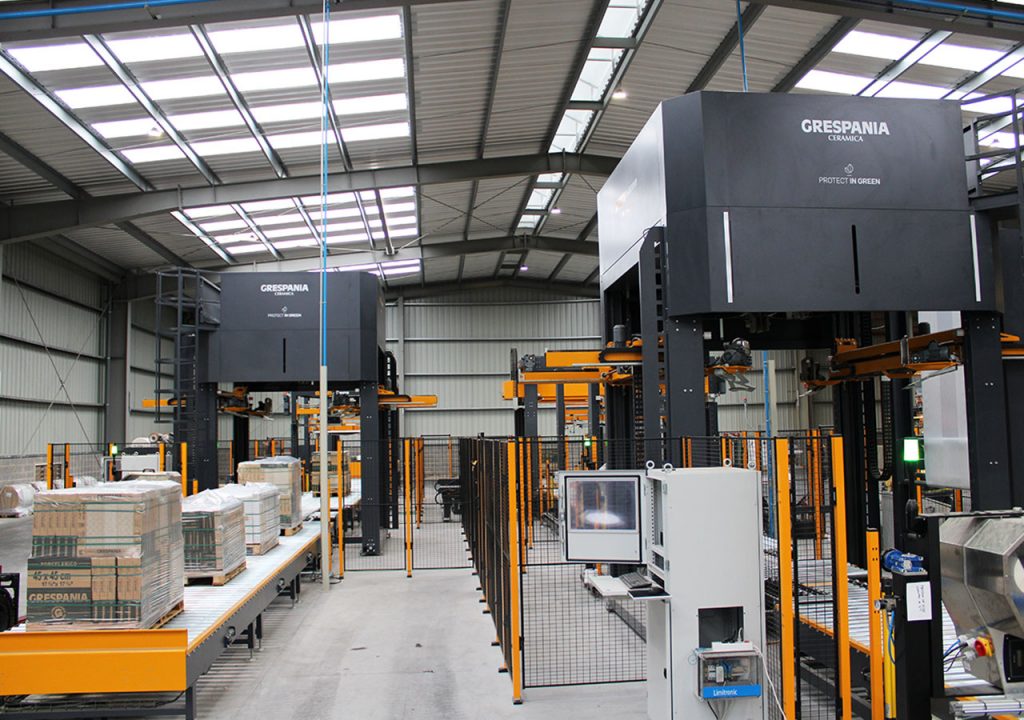
6. Autres aspects de projet d’emballage
Finalement, il est important de prendre en compte d’autres aspects de l’emballage lui-même qui n’affectent pas tant la conception de la ligne d’emballage, mais sa finalité. À ce stade, nous pourrions aborder des aspects tels que :
- Consommables : Définir les consommables qu’il sera nécessaire d’acquérir avec les nouveaux systèmes (cerclage, film, scellage, etc…).
- Installation énergétique : Une installation d’air comprimé est nécessaire pour tous les composants pneumatiques de la ligne. Si un système de thermorétraction est utilisé, une installation de gaz est aussi nécessaire.
En ce qui concerne l’alimentation électrique, il est nécessaire de connaître la fréquence, les volts, etc. de l’installation électrique de la machine.
7. Prévisions et projets futurs
D’autre part, il est important d’être clair sur les plans à venir concernant la production et/ou le conditionnement de l’usine afin de concevoir une ligne d’emaballage préparée pour de possibles agrandissements. Bien qu’il ne soit pas indispensable, il peut permettre d’économiser des coûts importants lors de l’extension de la ligne de production, car ce plan peut être utilisé pour plusieurs lignes de production ou formats autres que ceux proposés dans le projet initial.
Chez Innova, nous travaillons sur cet aspect dès le départ du projet, mais nous sommes aussi spécialisés dans les éventuelles extensions et modifications qui peuvent survenir dans l’avenir de la ligne.
En définitive, le client n’a pas besoin de connaître tous les aspects techniques du projet, mais les connaître l’aidera à bien définir et à optimiser les performances de sa ligne de conditionnement. N’hésitez pas à nous contacter si vous avez des doutes ou pour demander un devis sans engagement.