TOP 10 questions les plus fréquentes sur les systèmes de sécurité dans une ligne de banderolage
La sécurité sur les lignes de banderolage est un aspect fondamental pour protéger le personnel technique. Chez Innova, l’intégration des systèmes de sécurité dans un final de ligne ne se limite pas à se conformer aux réglementations en vigueur : elle est intégrée dès la phase de conception, afin de s’adapter à tout environnement et répondre aux besoins du client.
Dans cet article, nous vous présentons les 10 questions les plus fréquemment posées, en tant que fabricant de systèmes de banderolage, sur les éléments de sécurité d’une ligne : depuis ceux qui sont indispensables et obligatoires, jusqu’à ceux qui sont optionnels mais contribuent à améliorer la productivité de la ligne.
TOP 10 questions les plus fréquentes sur les systèmes de sécurité
- Quels systèmes de sécurité sont indispensables dans une ligne de banderolage?
- Quel type de signalisation peut être intégré aux systèmes de banderolage?
- Comment le panneau de commande contribue-t-il à garantir la sécurité?
- Que se passe-t-il si un opérateur entre dans la zone de travail pendant que la machine fonctionne?
- Comment la protection est-elle assurée pendant les tâches de maintenance?
- Que se passe-t-il en cas de panne ou de défaut de sécurité en pleine production?
- Peut-on adapter le niveau de sécurité selon l’environnement de travail?
- Comment les systèmes de sécurité s’adaptent-ils aux normes de chaque pays?
- Quelle formation le personnel doit-il recevoir en matière de sécurité?
- Comment la sécurité contribue-t-elle à améliorer la productivité dans une ligne de banderolage?
1. Quels systèmes de sécurité sont indispensables dans une ligne de banderolage?
Selon les normes internationales de sécurité au travail, une ligne de banderolage ou toute machine automatique doit disposer d’un périmètre de sécurité (généralement délimité par des barrières physiques ou photoélectriques), d’un système d’arrêt d’urgence, et d’un système d’alarme et de signalisation. Pour respecter ces exigences, certains éléments doivent être compris dans la ligne de banderolage.
Zone de sécurité :
- Clôture (Grillage) périphérique: Une clôture métallique qui délimite l’accès direct à la machine pendant son fonctionnement. L’accès intérieur ne peut se faire que par les portes de sécurité.
- Barrières de sécurité avec photo réflecteurs: En complément ou en alternative à la clôture. Elles sont souvent employées dans des zones accessibles lorsque la machine est à l’arrêt. Si la barrière est franchie lors du cycle, une alarme se déclenche et le système s’arrête pour des raisons de sécurité.
- Arrêts d’urgence accessibles : Boutons placés à divers endroits de la ligne permettant un arrêt immédiat en cas d’imprévu.
- Systèmes d’accès par clé ou boutons autorisés : Mécanismes de contrôle empêchant l’utilisation ou l’accès sans autorisation préalable.
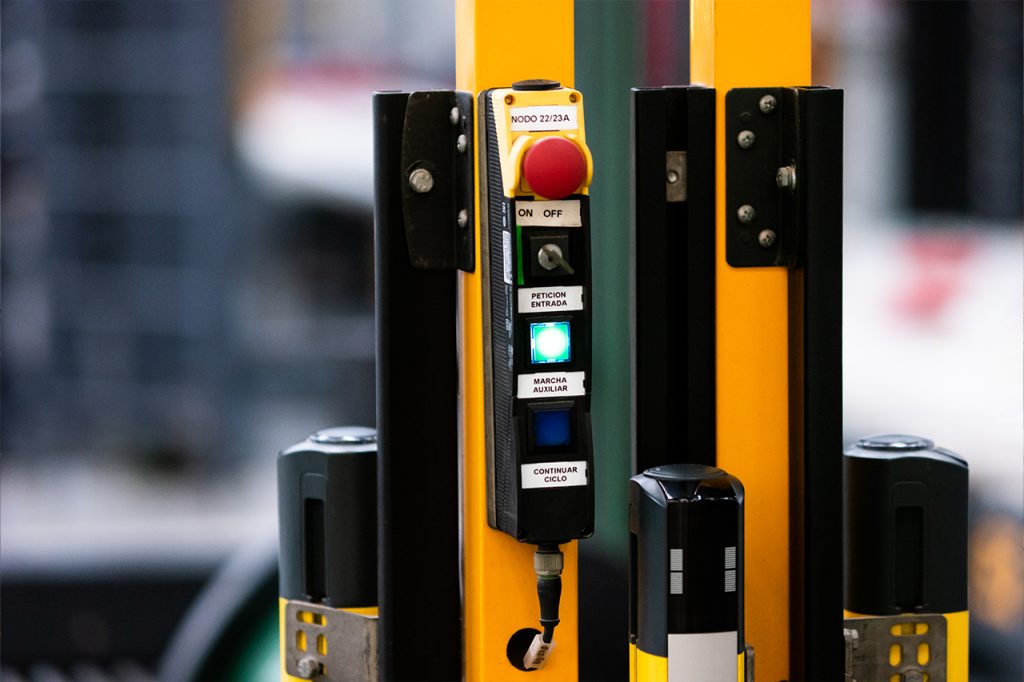
Contrôle de sécurité :
- PLC de sécurité (Programmable Logic Controller) : Surveille et contrôle tous les dispositifs liés à la sécurité, comme les arrêts d’urgence, barrières, capteurs de portes, etc. Il est programmé pour garantir une réponse rapide et maîtrisée à toute anomalie.
Signalisation de sécurité :
- Signalisation acoustique et lumineuse : Il est obligatoire de prévoir une signalisation en cas de panne, accident ou arrêt, via différents dispositifs, comme indiqué ci-dessous.
2. Quel type de signalisation de sécurité peut être intégré aux systèmes de banderolage?
Outre les dispositifs évoqués plus haut, un autre élément essentiel est la signalisation acoustique et lumineuse. Chaque type de signal a une fonction spécifique et ils sont souvent complémentaires:
Signalisation acoustique: Alarmes sonores indiquant le début d’un cycle, une défaillance mécanique ou l’ouverture non autorisée d’une porte.
Signalisation lumineuse : Balises signalant l’état de la machine. Par exemple : rouge pour alarme ou arrêt d’urgence, jaune pour situation anormale nécessitant attention, vert pour fonctionnement normal, bleu pour action spécifique à effectuer. Chez Innova, nous utilisons habituellement deux (vert‑rouge) ou trois couleurs (vert‑jaune‑rouge), selon la demande du client.
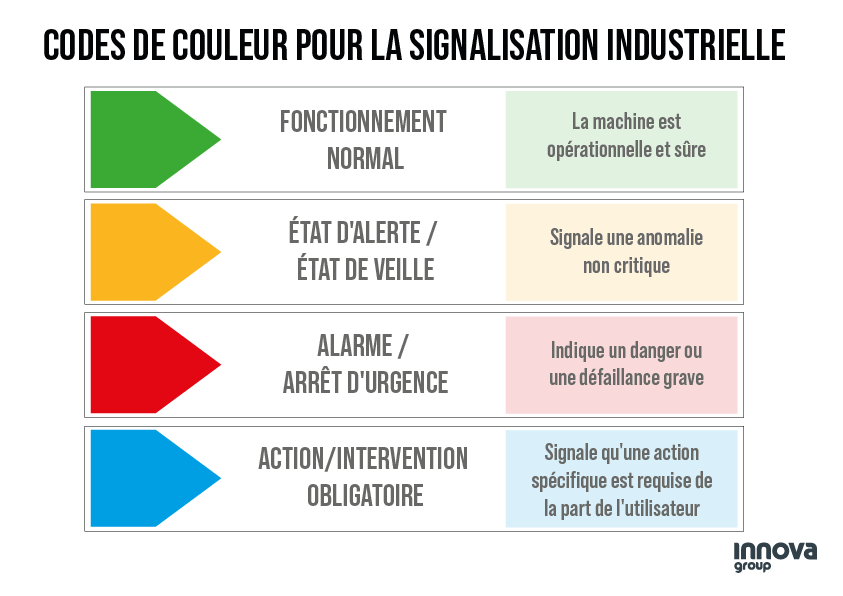
3. Comment le panneau de commande contribue-t-il à garantir la sécurité?
Le panneau de commande HMI est un outil essentiel pour la sécurité:
- Surveillance en temps réel de tous les dispositifs de sécurité.
- Affichage clair et priorisé des alarmes et incidents.
- Accès aux fonctions restreint par mot de passe ou clé électronique, empêchant toute manipulation non autorisée.
- Activation de modes sécurisés (maintenance, arrêt d’urgence).
- Enregistrement des historiques de panne, facilitant la traçabilité et la maintenance préventive.
- Connexion à distance pour assistance technique, favorisant une résolution sécurisée des pannes.
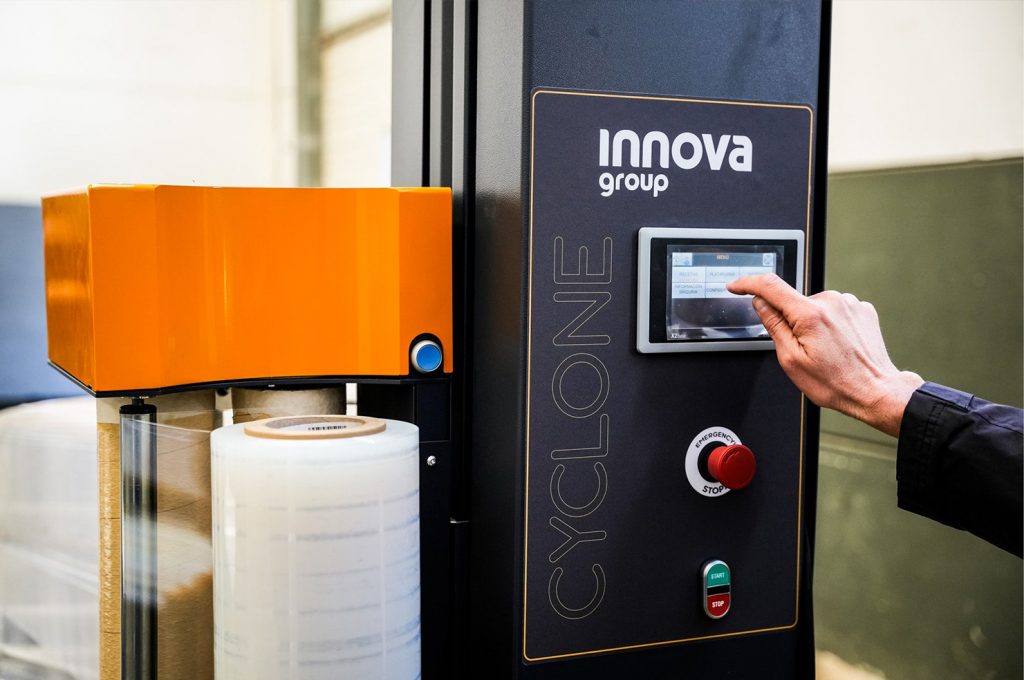
4. Que se passe-t-il si un opérateur entre dans la zone de travail pendant que la machine fonctionne?
Si un opérateur entre dans la zone pendant que la machine fonctionne, les systèmes de sécurité interrompent immédiatement le processus pour prévenir tout accident.
Cette réaction automatique est garantie par les dispositifs précédemment mentionnés : barrières photoélectriques, systèmes d’accès aux portes et PLC de sécurité détectant toute anomalie et arrêtant la machine.
5. Comment la protection des opérateurs est-elle assurée lors des tâches de maintenance?
Avant d’effectuer toute opération d’entretien, la machine doit être mise hors tension à l’aide d’une clé, le disjoncteur général doit être coupé et un cadenas doit être posé. À l’arrêt, les machines Innova disposent de systèmes internes antichute sur les composants mobiles : lorsque ceux-ci sont activés, des cylindres mécaniques de sécurité bloquent les pièces mobiles sur le châssis, protégeant ainsi le personnel technique.
Ces dispositifs entrent également en action lors de situations d’urgence, coupures électriques ou intervention sur les barrières.
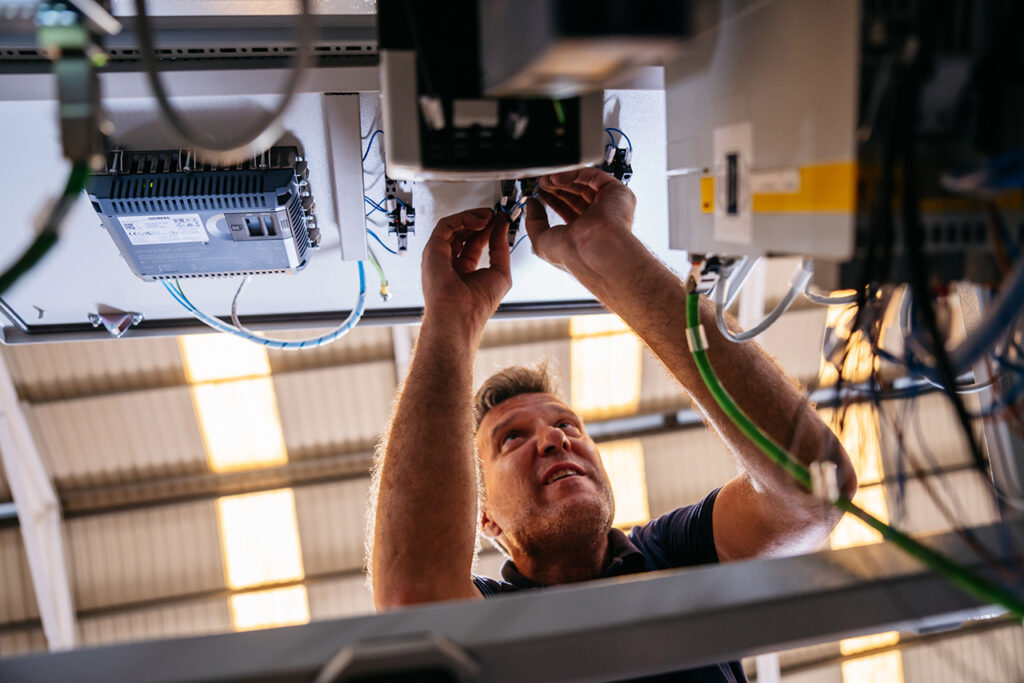
6. Que se passe-t-il en cas de panne ou de défaut de sécurité en pleine production?
Lorsqu’une panne est détectée, le PLC de sécurité arrête immédiatement la machine de façon sécurisée. En parallèle, la signalisation acoustique ou lumineuse s’active, plusieurs fonctions (y compris le système antichute) sont bloquées et une alarme s’affiche sur l’écran tactile.
L’opérateur voit clairement sur le panneau de commande la cause exacte de la panne, permettant une intervention rapide et sûre, réduisant le temps d’arrêt et minimisant les risques. Un diagnostic à distance est également possible pour une réaction encore plus efficace.
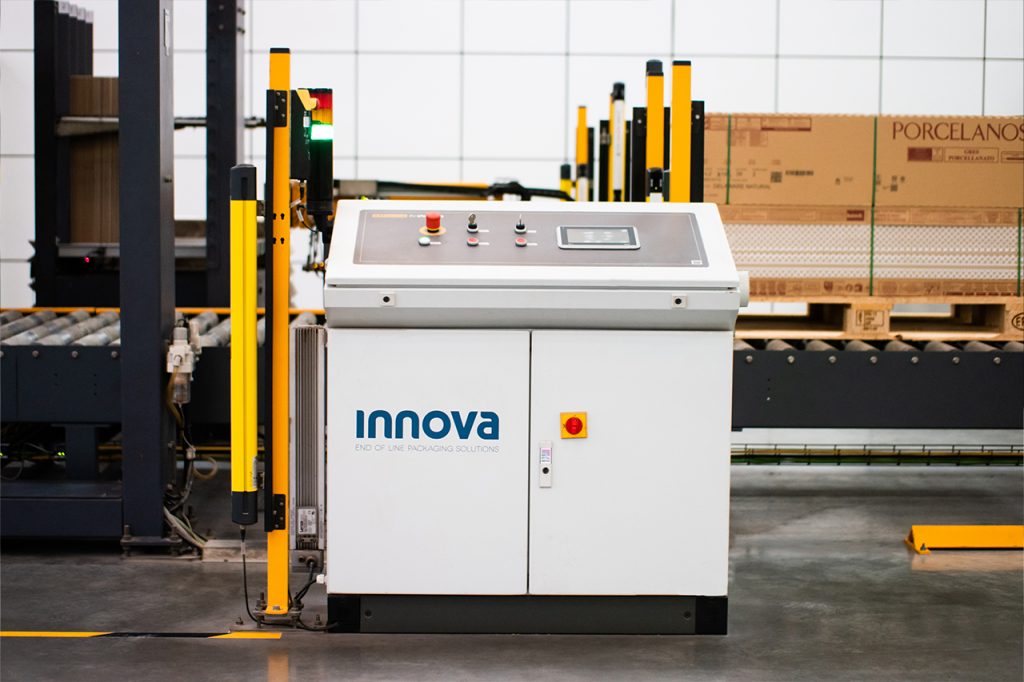
7. Peut-on adapter le niveau de sécurité selon l’environnement de travail?
Oui. Le niveau de sécurité peut être adapté aux conditions spécifiques. En phase de conception, l’équipe technique évalue les besoins de production et les conditions du milieu (humidité, poussière, températures extrêmes, espaces restreints) afin d’intégrer les mesures de sécurité appropriées.
8. Quelles sont les adaptations les plus courantes à des environnements ou besoins spécifiques?
Voici les adaptations les plus fréquentes:
- Barrières photoélectriques en cas d’espace réduit ou à la demande du client: De plus, dans les installations où d’autres machines sont proches ou l’espace est limité, les clôtures et les protections périphériques peuvent être modifiées afin de garantir un accès sécurisé à l’opérateur et une délimitation correcte des zones à risque.
- Accès spécifique pour la maintenance: accès par l’échelle de maintenance de notre Housseuse étirable, équipée de marches et de garde-corps spéciaux.
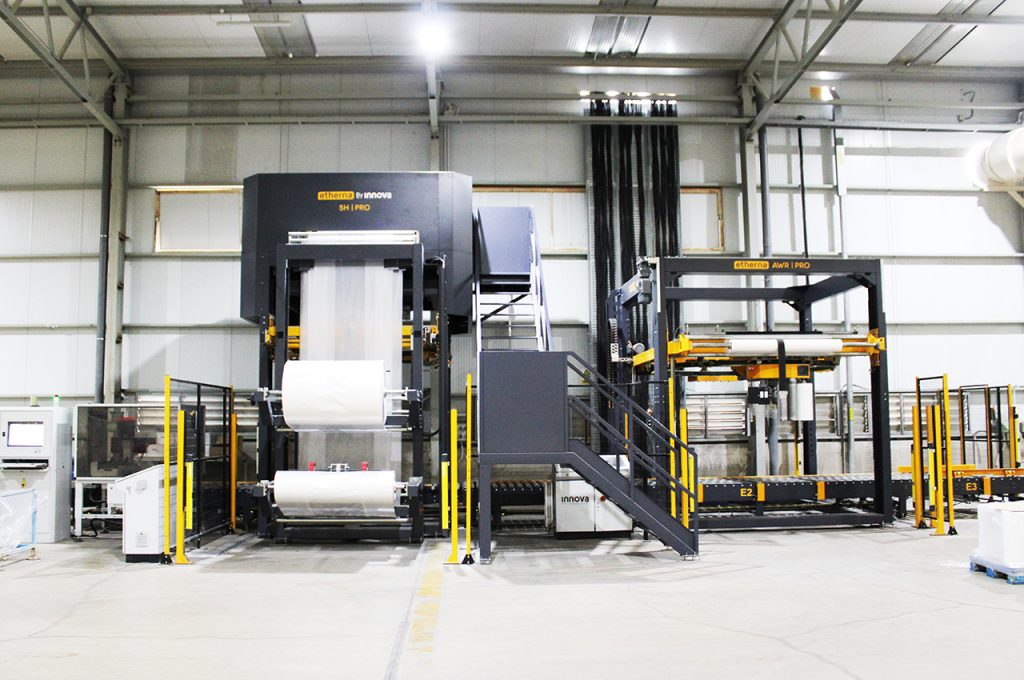
- Protection pour environnements spécifiques: utilisation de composants électriques IP65 ou IP67 en cas d’humidité, et installation de protections sur le châssis en atmosphère poussiéreuse ou ventilée.
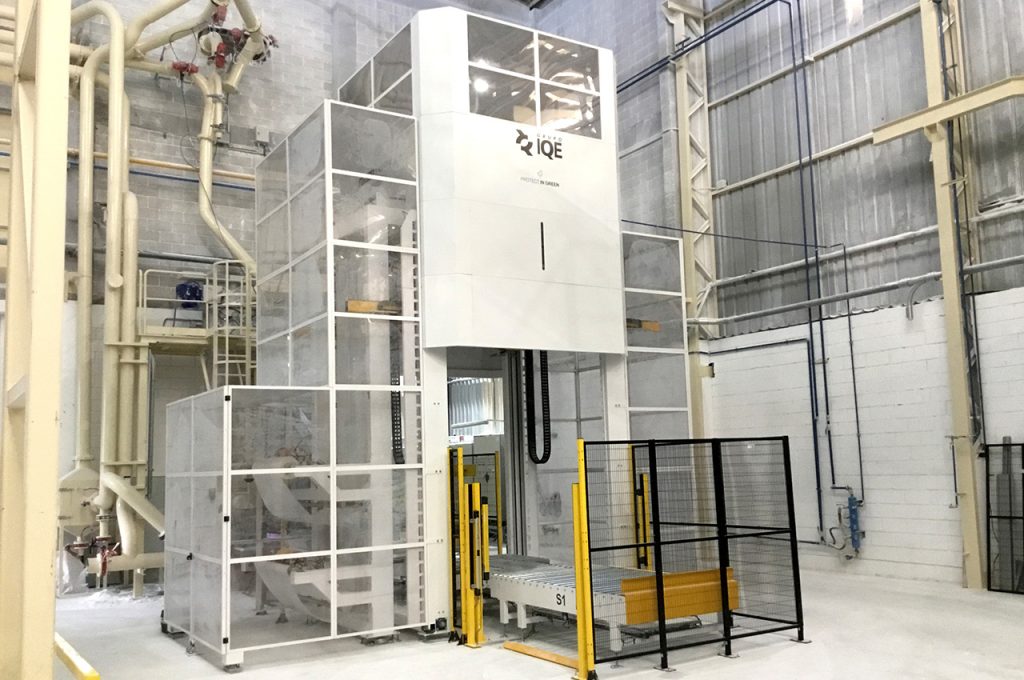
- Environnements de congélation ou corrosion: pour produits gelés ou corrosifs (sel, produits chimiques), on recommande des machines en acier inoxydable (INOX), résistantes à la corrosion et conformes aux normes d’hygiène strictes.
9. Comment les systèmes de sécurité s’adaptent-ils aux normes de chaque pays?
Chaque projet prend en compte les exigences nationales. Par exemple, en Europe, Innova conçoit ses systèmes conformément à la directive Machine CE 2006/42/CE. En plus des normes européennes, nos lignes et machines sont adaptées aux exigences telles que la norme NR12 (Brésil), UL (États-Unis) ou CSA (Canada).
10. Quelle formation le personnel doit-il suivre en matière de systèmes de sécurité?
Chez Innova, lors de l’installation d’une ligne, nous proposons une formation aux opérateurs et personnel technique, incluant la maintenance préventive, l’exploitation sécurisée, l’utilisation du panneau de commande, la reconnaissance des alarmes, etc. Des manuels techniques sont également fournis pour éviter les mauvaises pratiques et prolonger la durée de vie des systèmes.
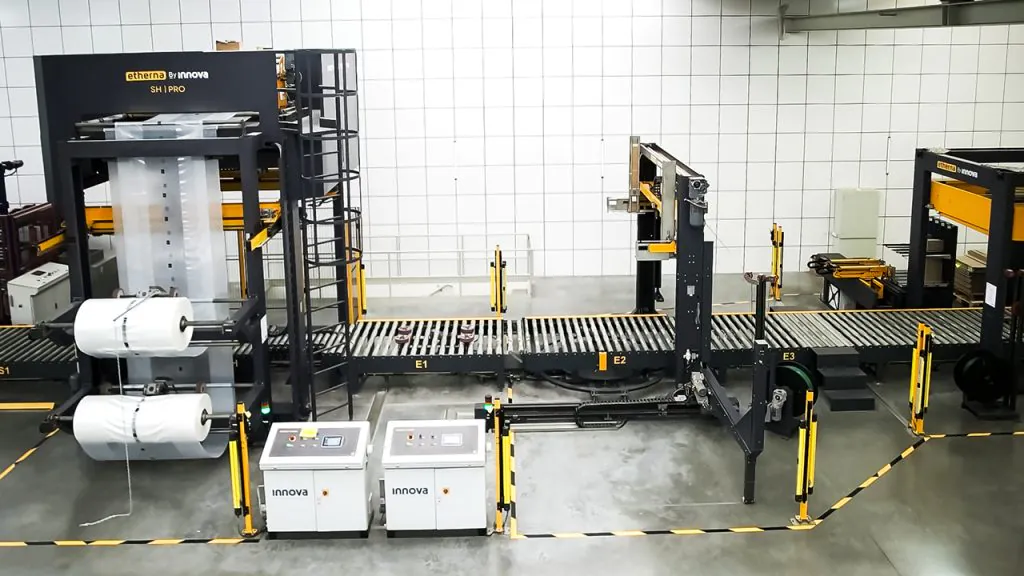
En bref, disposer d’un système de sécurité bien adapté et intégré ne protège pas seulement le personnel : c’est également un moteur d’efficacité et de productivité, en conformité avec les normes. Chez Innova, nous proposons des solutions sur mesure pour chaque client et secteur. Contactez notre équipe technique pour découvrir comment améliorer la sécurité et l’efficacité de votre final de ligne.